General News
19 February, 2025
Mount Isa recycling facility kicks into gear
The $20 million facility has begun processing recyclables from Mount Isa households.
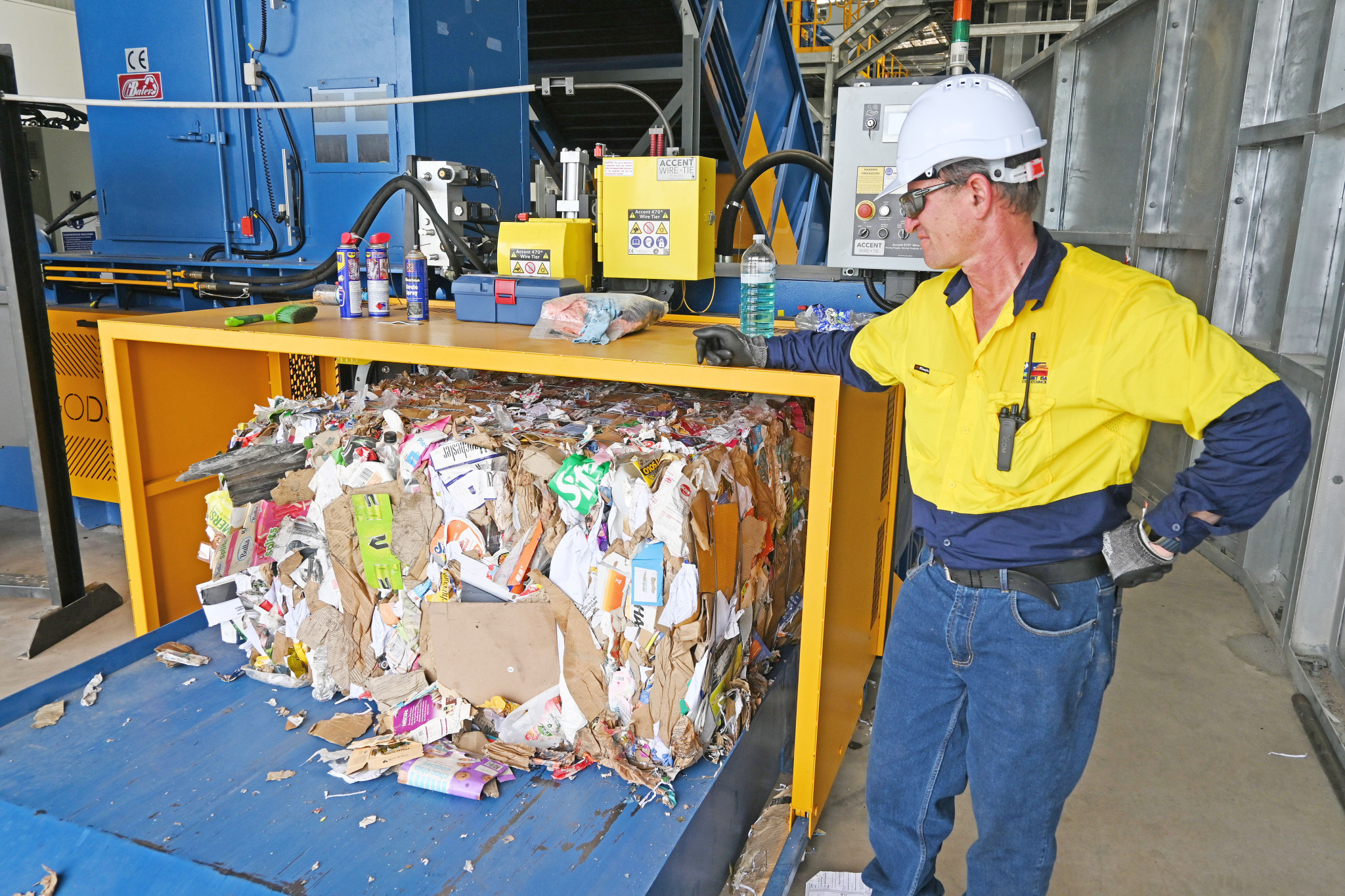
Mount Isa City Council has commenced processing at its $20 million Materials Recovery Facility (MRF).
The first recyclables began travelling along the conveyor belts, bunkers and balers late last week as council workers undertook training in the complex orchestra of machinery.
The council’s water and sewerage manager Chad King said the private contractors that built the facility will remain in control for the coming weeks as they conduct numerous test runs to ensure the end product commodity meets saleable standards.
“Material from the yellow bins is being processed and we are now checking that it is of a quality standard, for example, we are checking the plastics are not contaminated with other materials,” Mr King told North West Weekly.
“If you go to Woolworths or Coles, you’ll see they carry a lot of product with labels that say ‘made from 95 per cent recycled material’ – those manufacturers tend to get their materials from recovery facilities such as the one we now have operating in Mount Isa.”
So how does the recycling process work?
Firstly, trucks arrive daily at the facility after following the various collection routes across Mount Isa, including Camooweal, and unload several tonnes of material to be processed.
The recyclables initially travel through a pre-sorting point, where two workers hand-sort through rubbish travelling on a conveyor belt, looking for any hazardous material and removing it.
Council workers told North West Weekly that batteries, mobile phones, cans of paint and petrol and even a steel spike have already been wrongly placed into recycling bins.
The remaining rubbish then travels into a huge metal cylinder that contains holes of varying shapes that turn and separate the material according to size.
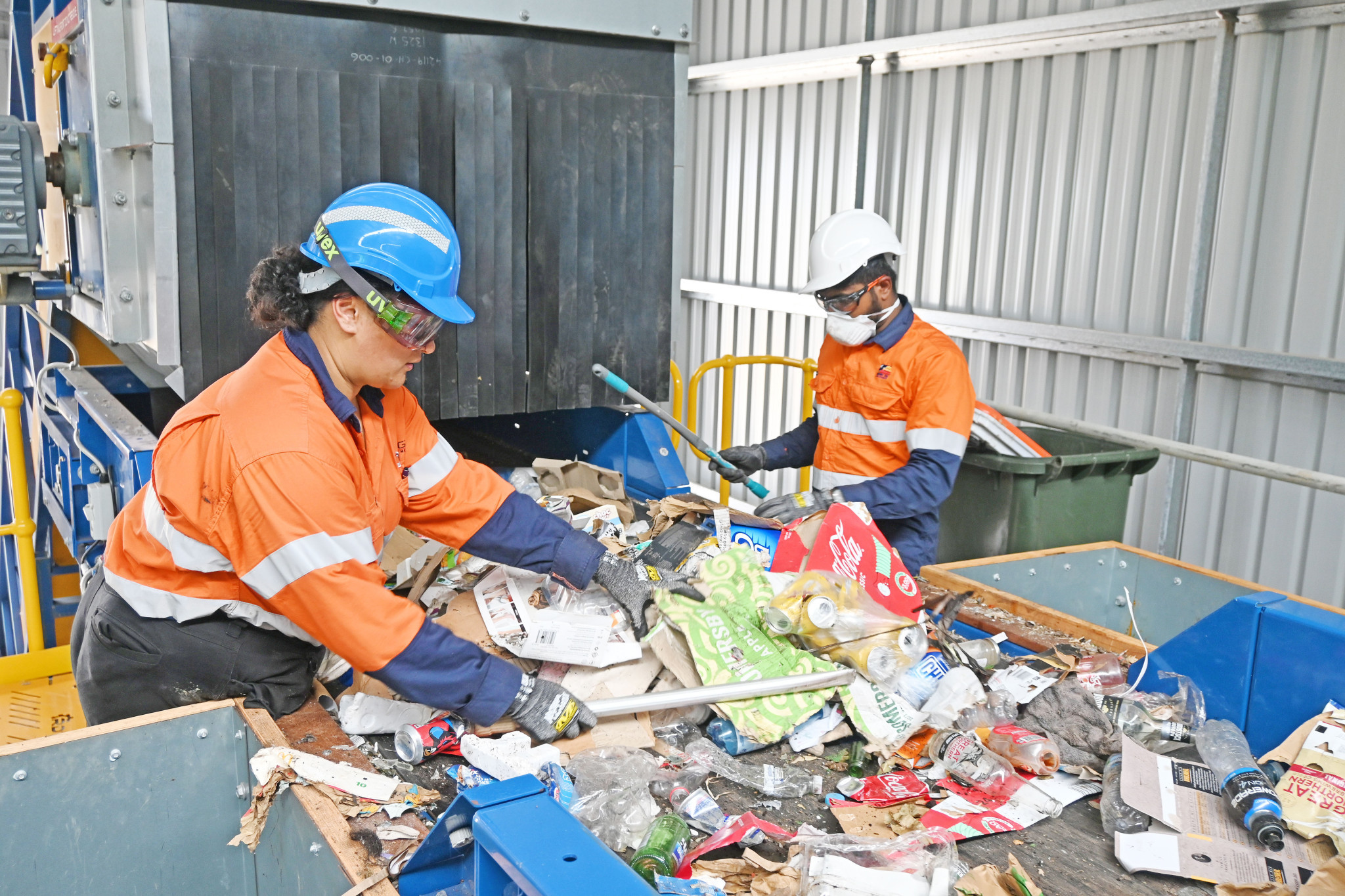
These items then travel past a large magnet that collects the aluminium and steel items, while plastics continue along the conveyor belt, passing by a high-speed camera that is connected to a database that contains more than 10,000 possible recyclable items that could be among the rubbish, based on a rapid scan of its shape and outline.
After being scanned, each item is then automatically dropped into a corresponding metal cage that gradually is filled with, for example, the exact same type of plastic.
When the large cage or ‘bunker’ is filled, the contents can be moved to a square baler machine that compresses the items into a bale about one metre high.
These bales of plastic, aluminium or steel can then be transported and sold to processing facilities seeking that specific commodity, similar to how someone might sell items to a scrap metal yard.
The machinery is currently working at a slower speed, but about three tonnes of recyclables will be processed each hour when operating at full capacity.
“As a new facility, we need to be able to prove we can meet certain quality targets so we can have a saleable commodity,” Mr King said.
“Part of meeting the quality standards of the commodity we produce is driven by the machinery at the materials recovery facility and partly it is also driven by how good we are as a community at putting the right thing in the right bin.”
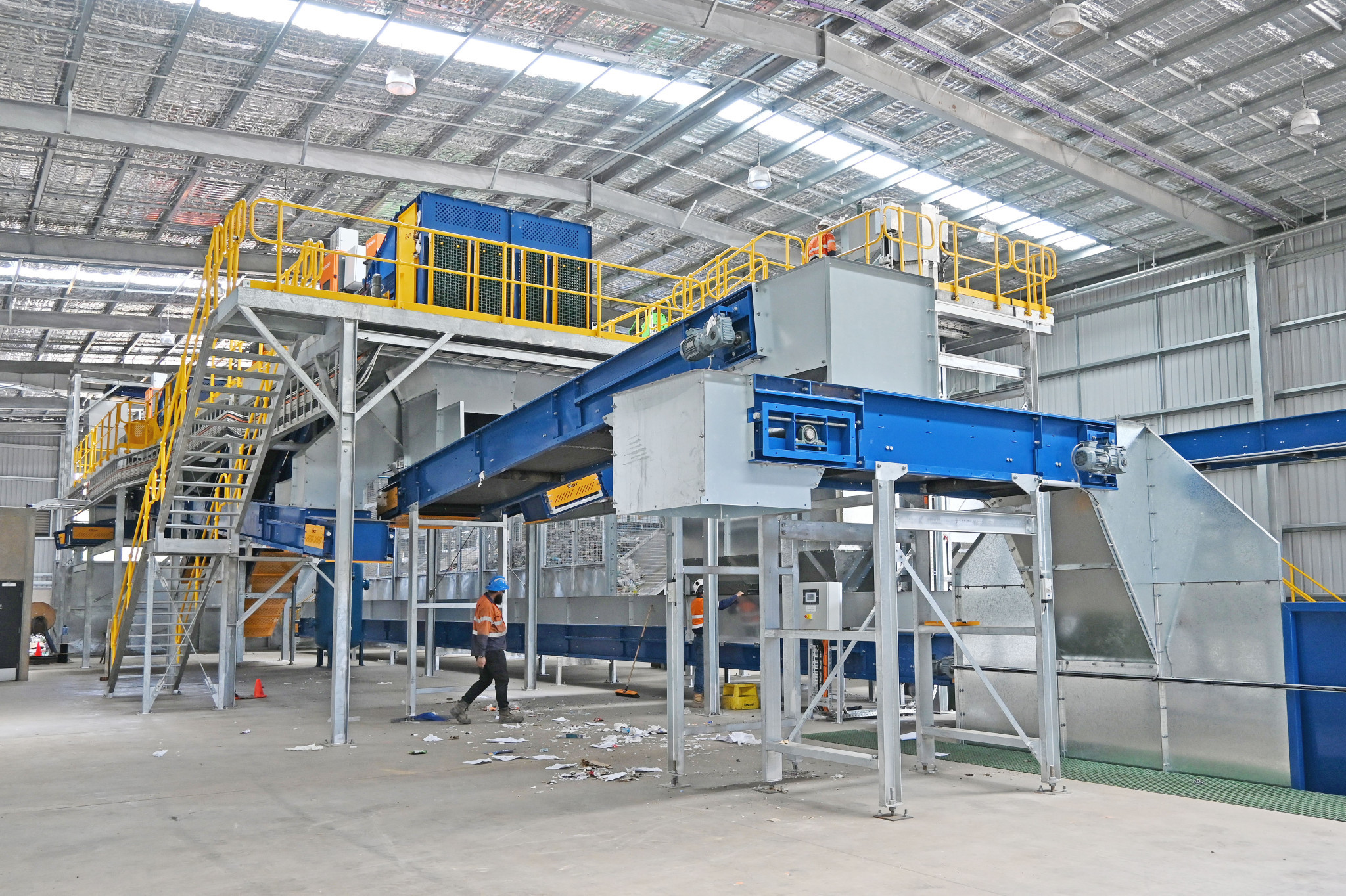